Portable, wearable and adaptable technologies are now the norm. As a result, the PCB’s required need to be smaller yet still capable of performing ever-more-complex functionality with smaller components. As PCB designers we are continuously challenged to meet these requirements by using the most effective placement of components and PCB Layout as possible without affecting its electronic capabilities.
As a result, PCB Layout becomes a critical part of any design.
Not got time to read this now?
Fill in the form below and we will send you this article and others like it via email.
Begin with the end in mind
Prioritising the most important requirements can help streamline the design process by determining the constraints on the design. Sizing and placement of critical elements, including minimum and maximum tolerances, required components, electrical demands including impedance factors and power needs all combine to generate an initial set of constraints for the PCB design.
PPPPP (proper planning prevents poor performance)
It’s also a good practice to create and save sets of like constraints and templates for subsequent designs or projects. Having time-proven templates available can streamline the design of new boards or upgrades to existing PCBs. Once constraints are set and understood, it makes the details much less error-prone, saving time and money.
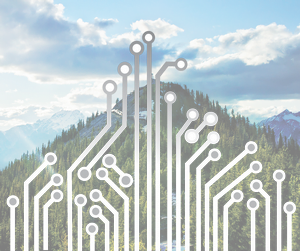
Board layout techniques can include such strategies as devices embedded on inner layers of PCBs to reduce board size. This must be evaluated with manufacturers to verify that these capabilities can be met in actual fabrication.
Errors or lack of planning in the layout specification of PCB design can cause multiple problems:
• Manufactured products that don’t perform as specified or designed
• Quality or functional issues may surface due to components and circuit paths that conflict with other board elements from factors such as electromagnetic interference, current flow, track width, component size, and physical board limitations.
• Boards may not be able to be manufactured exactly as specified, resulting in back-and-forth decisions between the designer and manufacturer. This extends lead time and increases cost.
• Worst case – the engineer goes back to the “drawing board” to rework the design for manufacturability.
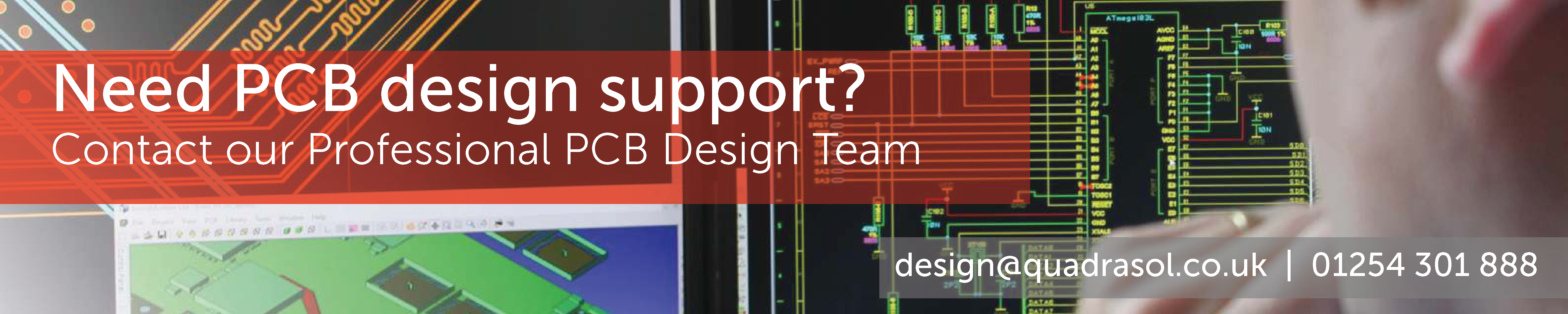
Design for Manufacture
Obviously, the main aim is to create a board that can be efficiently and cost-effectively manufactured. Understanding the manufacturing process is a real benefit as it enables the engineer to comprehend how fabrication methodology will react to their designs. Multi-layer boards and double-sided laminates or double-sided component placement designs can make the layout all the more critical in designing for manufacturing (DFM). IPC CID Training can also help guide some of these layout decisions.
An effective tool available to PCB designers prior to prototype creation is DFM software . Such tools analyze the designer’s files and evaluate them for any issues or omissions related to fabrication. Combining the use of PCB design tools and DFM applications is the best solution to designing PCBs of the highest quality that will be functional and cost-effective to manufacture.
It’s also important to work with a fabricator who provides extensive support of all technical aspects of PCB orders, including a detailed review of submitted designs with CAM tools.
For more information about our IPC CID Trained PCB Design Team and our PCB training and supporting software please contact us.
For more information please contact us today!